Clean Future speaks with Danish Rashid, General Manager – North & Head, GBMC at ACC Limited about the success of their environment friendly and sustainability initiative to create a community of 600 green building material manufacturing partners across the country by 2025.
What is Green Building Centers and what makes green building materials better than the traditional materials?
ACC’s Green Building Centers is company’s initiative to facilitate low-cost, housing development in India, through promotion of sustainable materials, building techniques and locally trained workforce. The production of green building materials at Green Building Centers (GBCs) is carried out in a modern production environment with main emphasis on Quality & Service.
A Quality Assurance Test Laboratory in every Green Building Center ensures strict quality checks of Incoming raw materials & Outgoing products. As a result, GBCs produce building materials of superior quality as against traditional materials. Customers benefit from the quality of Green Building Materials due to reduced application cost & durability.
In traditional brick kilns, the fertile top soil is used for the production of red bricks which makes the land infertile. The use of coal in firing of red bricks causes pollution. Green building materials are eco-friendly and promote sustainable development while fly ash bricks reduce CO2 emissions, conserve natural soil and utilize waste.
What prompted ACC to start this initiative?
ACC set up Green Building Centers, in 2013, to promote affordable construction solutions, as a “one-stop shop” in smaller towns and semi-urban clusters to establish an ecosystem for affordable housing, sanitation & providing our consumers solutions beyond cement. This initiative provides an opportunity to channel partners to grow their business, and catalyze rural development.
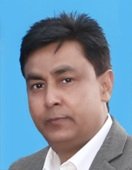
The main objectives of GBC is triple bottom line approach in business development and establishing centers of excellence, which will have an positive impact on sanitation through affordable eco-friendly products and also moving beyond products to solutions.
What is the business model for these centers?
ACC’s GBCs enable distribution of low cost,, local and environment-friendly building materials and solutions with opportunities for training and creating livelihoods. We provide technical and marketing support required to establish the business model and are operated under the supervision of ACC in terms of layout, safety measures, machine capacity and design, quality control labs, etc.
By supporting partners to establish various linkages, ACC ensures that the center reaches out to different types of customers.
What has been the environmental impact of this initiative?
The Green Building Centers positively impact the climate, water and nature as well as the communities at large. The environment impact can easily be measured along the following parameters:
Saving in CO2 emission: A total of 183 MT of CO2 emission is saved when a million Fly Ash Bricks are used instead of Red Bricks. Fly Ash Bricks save 30% of the fuel that is used in firing red bricks. It is estimated that in India red bricks produce 22% of the CO2 produced by the construction sector , and this can be saved by the use of Fly Ash Bricks ,
Fertile Top Soil Conservation: 2.6 Kg of fertile soil is saved for every Fly Ash Brick used in construction. Annual consumption of Red Bricks is estimated to be 240 billion, and the use of Fly Ash bricks provides a vast opportunity for saving fertile agricultural soil.
Utilization of Waste Materials: Every fly ash brick utilizes 1.6 kg of fly ash. Fly ash is an industrial waste produced in large quantities in coal based thermal plants, which is an essential component of cement.
ACC GBCs use blended cement for the manufacture of Concrete Products. Blended cement conserves natural resources and reduces greenhouse gas emissions associated with cement production. It also produces more durable concrete products than Ordinary Portland Cement (OPC).
How has been the journey so far?
The journey so far has been good as several partners across the country today share our vision of the triple bottom line approach and Sustainable development. This ecosystem for affordable housing and sanitation has been able to contribute to a greener world by protecting fertile topsoil, controlling CO2 emissions, improving the livelihood for people, utilizing waste materials and creating opportunities for employable skills based training and development.
GBCs have been stabilizing and scaling up their operations. As a result, many more partners are joining the GBC initiative.
The footprint is expanding rapidly with partners being added in all regions. By the end of 2025, we aim to have approximately 600 partners around the country.
What is the impact of GST on your product? Will it increase or decrease the prices?
We don’t expect GST will have any kind of severe impact on pricing, as prior to GST, a VAT of 5% along with Excise Duty depending on the size of unit was levied on products and now it has now been replaced by 12% GST.